На предприятиях пивоваренной отрасли наибольшее распространение получили кизельгуровые фильтры: они надежны, просты в устройстве и экономически выгодны.
Однако существует ряд проблем, связанных с использованием кизельгура: ограниченность ресурсов высококачественного диатомита, а также большие расходы на утилизацию. Поэтому в настоящее время ученые сосредоточили усилия на следующих направлениях: поиск новых методов регенерации кизельгура; использование альтернативных материалов и оборудования для фильтрования.
При использовании в среднем 1 кг кизельгура на 30 л пива ежегодно производится несколько тысяч тонн кизельгурового шлама, который предприятия за собственные средства должны утилизировать. Однако проблема состоит в том, что кизельгуровые отходы ввиду значительного количества связанного азота могут привести к накоплению в земле и воде нитратов [1, 2].
Одним из перспективных направлений является термическая регенерация кизельгура. При этом образуется материал, который снова может использоваться для фильтрации пива. Однако высокие температуры ведут к качественным изменениям продукта. Доля пригодного кизельгура составляет, в большинстве случаев, малую величину. Поэтому разработка тепло- и ресурсосберегающего способа термической регенерации кизельгура, режимные параметры которого обеспечивают высокие качественные показатели регенерируемого кизельгура с точки зрения его повторного использования в процессе осветления пива является актуальной задачей [3, 4].
Целью работы является научное обеспечение и разработка способа термической регенерации кизельгура для повторного его использования в процессе осветления пива и разработка инновационных технологических и конструкторских решений при практической реализации процесса.
Материалы и методы исследования. Проведение экспериментальных исследований пиролиза кизельгурового шлама обусловлено необходимостью выявления закономерностей термического разложения органических составляющих в условиях ограниченного доступа кислорода. Исходя из этого для более точного осуществления процесса и возможности изучения влияния отдельных факторов на эффективность проведения процесса без возмущающих неконтролируемых воздействий сопутствующих факторов эксперименты осуществлялись на специально сконструированной установке периодического действия.
В состав схемы экспериментальной установки (рис. 1) входят следующие элементы: вертикальный пиролизный реактор с рубашкой 1, двойная шиберная заслонка 2, горелка 3, воздушный кожухотрубчатый конденсатор 4, вентилятор 5, емкость – сборник жидкой фракции 6, каплеотбойник 7, фильтр 8 и вентилятор 9. Все элементы установки соединены между собой системой трубопровода 10 и крепятся на раме 11. Трубопровод между реактором и конденсатором снабжен сбросным клапаном, на этом же трубопроводе расположена термопара для измерения температуры выходящей парогазовой смеси. Для обеспечения и контроля заданного режима утилизации и безопасного проведения эксперимента внутри реактора также располагается термопара.
Рис. 1. Схема пиролизной экспериментальной установки:1 – пиролизный реактор, 2 – двойная шиберная заслонка, 3 – горелка, 4 – конденсатор, 5 – вентилятор, 6 – емкость сборник, 7 – каплеотбойник, 8 – фильтр, 9 – вентилятор, 10 – система трубопровода, 11 – рама
Реактор (рис. 2) в свою очередь состоит из следующих основных элементов: корпус реактора 1, рубашка 2, выгружатель 3, патрубок парогазовой смсси 4, патрубок топочных газов 5, нижний патрубок рубашки 6, фланец байонетный 7. Снаружи корпус реактора 1, выполненный из стали 08X181110 Г, снабжен рубашкой 2, внутри которой циркулируют продукты горения топлива, обогревающие реактор и обеспечивающие процесс пиролиза. К рубашке 2 приварены опоры, с помощью которых реактор устанавливается на раме. К фланцу корпуса сверху крепится двойной шибер, через который производится загрузка сырья.
Рис. 2. Пиролизный реактор:1 – корпус реактора, 2 – рубашка, 3 – выгружатель, 4 – днище, 5 – патрубок парогазовой смеси, 6 – патрубок топочных газов, 7 – нижний патрубок рубашки, 8 – фланец байонетный
К фланцевому соединению нижнего патрубка рубашки 7 тангенциально крепится горелка, продукты сгорания от которой служат для обогрева реактора 1.
Для удаления из системы, поднимающегося снизу вверх потока топочных газов в рубашке 2 служит патрубок топочных газов. В нижней части реактора смонтирован выгружатель 3. Установка периодического действия, поэтому во время работы разгрузочное устройство закрыто байонетным фланцем 8. Для разгрузки зольного остатка предназначен шнековый выгружатель 3. Для отвода из реактора 1 парогазовой смеси, полученной в процессе пиролиза, установлен верхний патрубок 5. Кроме этого, для исключения тепловых потерь в окружающую среду и обеспечения безопасности при работе с установкой, снаружи реактор предусмотрена теплоизоляция в виде листов минеральной ваты.
Результаты исследования и их обсуждение. Для близкой имитации промышленной переработки кизельгурового шлама пивоваренного производства после серии опытов с загрузкой в реактор небольших объемов пиролизная установка была опробована при циклической загрузке с возможным заполнением на половину реактора. Устанавливаемая температура в реакторе 450 °С. Полученные результаты приведены в табл. 1.
Таблица 1
Значения параметров проводимого процесса
Продолжительность цикла, мин |
t, °C в реакторе |
t, °C парогазовой фракции |
t, °C в сборнике |
t, °C выходящих газов |
t, °C топочных газов |
|
Вид сырья |
Отработанный кизельгур |
|||||
1 |
0 |
467,9 |
61,2 |
25,7 |
23 |
65,7 |
2 |
30 |
450,9 |
101,1 |
26 |
25,5 |
62,5 |
3 |
60 |
451,2 |
94,1 |
26 |
27,4 |
67,8 |
4 |
90 |
427,7 |
103,7 |
25,5 |
29,4 |
70,5 |
5 |
120 |
441,8 |
94,9 |
25 |
32 |
72,3 |
6 |
150 |
465,8 |
90,2 |
24,7 |
31,5 |
71,5 |
7 |
180 |
457,3 |
83,4 |
24,8 |
30,9 |
70,4 |
8 |
210 |
432,5 |
104,8 |
24,9 |
31,9 |
71,3 |
9 |
240 |
433,6 |
113,2 |
24,9 |
34,1 |
70,2 |
10 |
270 |
463,1 |
96,8 |
24,8 |
32,8 |
69,7 |
11 |
300 |
442,5 |
92,8 |
25,1 |
32,8 |
68,9 |
12 |
330 |
428,5 |
103,5 |
25,2 |
33,6 |
67,6 |
13 |
360 |
452,7 |
110,7 |
25,1 |
31,8 |
64,3 |
Итого: |
360 |
– |
– |
– |
– |
30 |
На рис. 3 представлена графическая зависимость температур выходящих продуктов и температуры в камере во время процесса пиролиза, а на рис. 3 влияние различных факторов на процесс пиролиза.
Рис. 3. Зависимость температур пиролиза от времени процесса
В процессе каждой загрузки наблюдалось небольшое падение температуры в реакторе при внесении новой порции сырья. А также происходило колебание в процессе пиролиза температуры парогазовой фазы.
При выгрузке продуктов из пиролизной установки было заметно, что часть сырья осталась не переработанной (рис. 5).
Рис. 4. Зависимость показаний ДМЦ от времени процесса
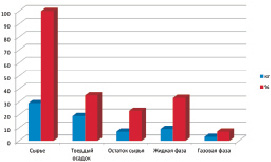
Поэтому для исследования в лаборатории было взято несколько проб. Полученные результаты представлены в табл. 2.
Таблица 2
Данные лабораторного исследования
Материал |
Масса исходная, г |
Масса влаги |
Органика (летучие) |
Остаток (неорганика) |
|||
г |
% |
г |
% |
г |
% |
||
Отработанный кизельгур |
1,37 |
0,97 |
70,8 |
0,07 |
5,1 |
0,33 |
24,1 |
Переработанный остаток |
1,683 |
0,35 |
20,8 |
0,053 |
3,15 |
1,28 |
76,05 |
Не переработанный |
2,047 |
1,06 |
51,8 |
0,09 |
4,38 |
0,897 |
43,82 |
Чистый кизельгур |
0,3 |
0,1 |
33,3 |
0,05 |
16,7 |
0,15 |
50 |
Заключение
В переработанной части остатка доля сухого остатка преобладает, по сравнению с чистым сырьем влаги в этом продукте намного меньше. Однако в не переработанном остатке, как и в исходном сырье, большую часть составляет влага.
Работа представлена на Международную научную конференцию «Актуальные вопросы науки и образования», Россия (Москва), 21-23 мая 2012 г. Поступила в редакцию 22.06.2012.