Введение
Разработка угля современными лавами при несовпадении мощности пласта и вынимаемой мощности механизированных комплексов приводит к существенным его потерям. Это особенно очевидно в условиях обострившейся конкуренции, когда производители стремятся развить максимальную скорость выемки, применяя комплексы в благоприятных условиях, не считаясь с потерями угля. Поэтому лавами не эффективна отработка пластов имеющих сингенетические нарушения (возникают на возвышенных участках древнего рельефа, где торф отсутствовал, а также за счёт неравномерности опускания или поднятия отдельных участков при наличии карстовых отложений) и угольных пластов с торфодоломитовыми конкрециями с высокой механической прочностью [2, 3]. При встрече с такими нарушениями возможно прекращение добычи и демонтаж тяжёлой дорогостоящей техники. Такое, например, имело место на ш. Казахстанская в Караганде при эксплуатации комплекса Glinik. С учётом таких факторов пласты относят к забалансовым, т.е. не пригодными к добыче, см., например, «Концепция развития угольной промышленности Республики Казахстан на период до 2020 года», таблица 1.
Таким образом, учитывая факторы изложенные в [1], можно сделать вывод, что упор на лавные технологии в условиях монополизации продаж механизированных комплексов и существующей системе поставок угля привёл к существенному подорожанию подземной добычи и распространению технологий наносящих большой ущерб экологии. Стремление уменьшить потери угля и вовлечь в добычу сложно залегающие месторождения приводит к схемам выемки с уменьшенной длиной лавы и увеличенным коэффициентом раздвижности крепи (отношение вынимаемой мощности пласта к рабочей податливости) [3], а также к новым схемам короткозабойной выемки. При этом станет реальной разработка запасов, оставленных мощных угольных пластов К12 и К10, К2 Карагандинского бассейна и запасов представленных в таблице 1. Исследования и опыт отработки межтрековых целиках, показали, что эффективной системой их выемки является камерная. Недостатки использованных раннее таких систем в том, что годовая добыча не превышала 100-150 тыс. тонн в год, при потерях до 40-50%. Но производительность труда рабочего по добыче, из – за мало операционности и гибкости процесса добычи достигала 70 т/месяц.
Таблица 1
Забалансовые запасы на некоторых основных месторождениях Казахстана
Область |
Показатели, млн. тонн |
|
балансовые |
забалансовые |
|
1 |
2 |
3 |
Алматинская |
936,9 |
9975,3 |
Карагандинская |
10065,0 |
4446,8 |
Костанайская |
7535,9 |
12081,6 |
Павлодарская |
11920,0 |
1798,4 |
Конструктивные решения
Многовариантное проектирование и исследование таких систем привели к общей проблеме расчета и моделирования новых рычажных конструкций. Так для уменьшения количества единиц оборудования и операционности работы предложен угловой скребковый конвейер, обеспечивающий транспортирование угля из забоя, что позволяет устранить перегрузку вынести соответствующее оборудование за пределы выемочного участка, рис.1.
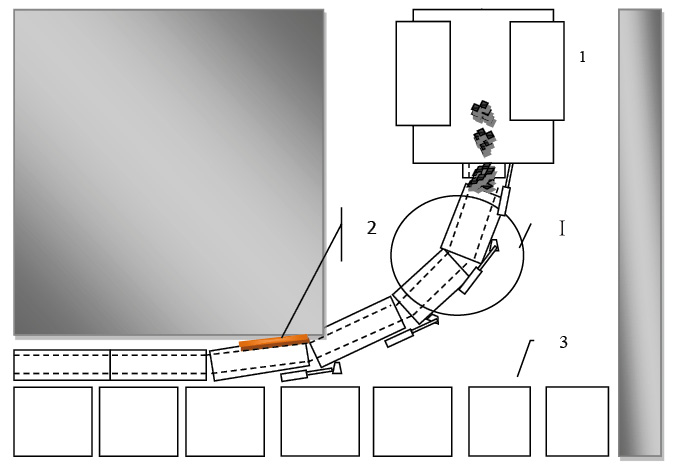
Рис. 1. Угловой скребковый конвейер на сопряжении: 1 – привод с группой рештаков; 2 – передняя опора комбайна; 3 – секции крепи
Конвейер имеет группу шарнирно соединённые рештаков. В группе рештаков через один рештак его средние листы, разделяющие полость на рабочее и холостое отделение, выполнены с торцов с прикреплёнными к их нижней или верхней поверхности упругими сегментами, заходящими под соседний лист (или заходящими над соседним листом), в полости холостой (или рабочей) ветви таким образом, что бы длина внешней дуги упругого сегмента при развороте рештаков на максимальный угол поворота для изменения направления транспортировки, предотвращала просыпание груза из рабочей в холостую полость. Рештаки в группе вертикальной осью вращения соединены между собой. А угол их поворота регулируется с помощью гидроцилиндров с гидравлически запираемыми, штоковыми и поршневыми полостями, при этом запирание осуществляется после фиксации группы рештаков в заданном положении; рештаки в группе, могут иметь пластинчатые направляющие для удержания цепи и скребков в зоне поворота от отклонения от расчётной траектории движения под действием отклоняющей силы тягового усилия цепи [5]; Для различных технологических схем их применения необходимо определить силовые характеристики нагружения конструкции в зоне поворота. Конструктивные и технологические изменения требуют создания новых методик расчёта обновлённого оборудования. Так на рис. 2 представлена схема демонстрирующая возможности изменения вынимаемой мощности пласта в более широких пределах (с повышенным коэффициентом раздвижности для крепи типа Glinik). В данном случае также следует выяснить характер изменения нагруженности крепи в зависимости от взаимного расположения звеньев, включая и углы предварительного наклона гидростойки. Следует учитывать и то, что изменение нагруженности может также произойти от перераспределения давления обрушенных пород на крепь. Опыт такого применения известен для крепи 2МКМ и 3МК, в 80-е годы, выпуск которых в СССР был налажен гораздо раньше, чем Glinik.
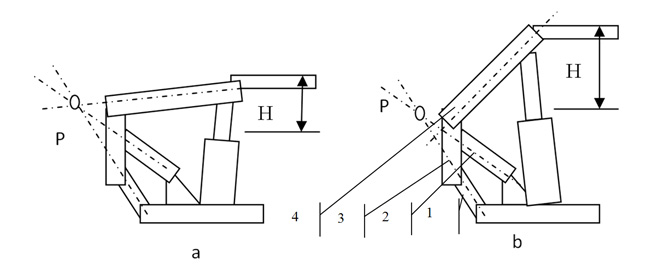
Рис. 2. Повышение коэффициента раздвижности: а – стандартная раздвижность; b – увеличенная; P – мгновенный центр вращения; 1 – нижний рычаг; 2 – верхний рычаг, 3 – ограждение; 4 – перекрытие.
Моделирование и исследование
Расчёт усилий, в узлах, скоростей и ускорений при движении звеньев основан на решении систем уравнений равновесия, для опорных реакций в узлах и реализован в системе языка VBA Excel [6], а также на основе известного пакета авто проектирования ADAMS. Его применение в КарГТУ малоизвестно и особенно для углового конвейера. Ещё меньше сведений о сопоставлении полученных на его основе результатов с практикой, чем и вызвана необходимость иметь дополнительные программы для проверки. Модели оборудования собираем из твёрдых тел, соединений (шарниры вращения и поступательного движения) и силовых факторов.
Для крепи анализ усилий по осям Х, У, при смешении секции (рис. 3) показывает, что при изменении угла между перекрытием и ограждением, верхний и нижний рычаги лемнискатного механизма нагружены в противоположные стороны с максимальным по абсолютной величине значением при пересечении осями рычагов и перекрытия точки Р, являющейся мгновенным центром вращения.
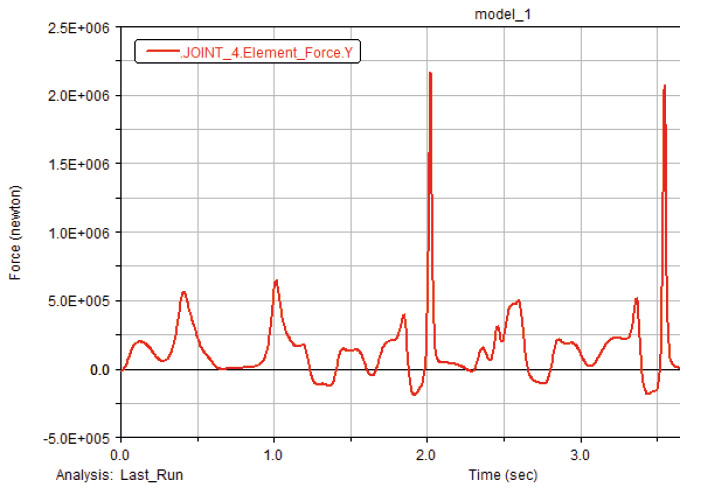
Рис. 3. Фото с экрана: изменений опорных реакций в шарнире верхнего рычага
Как следует из рис. 2 в положении b нагрузки в рычагах могут уменьшится, конечно общая величина давления пород на крепь может увеличится, из-за увеличения вынимаемой мощности пласта, однако факты возможности снижения нагрузки на рычаги за счёт оптимального взаимного расположения элементов крепи при повышении коэффициента раздвижности подтверждают возможности применения таких схем. На рис. 4 представлена идеализированная схема для расчета опорных усилий в скребках углового конвейера.
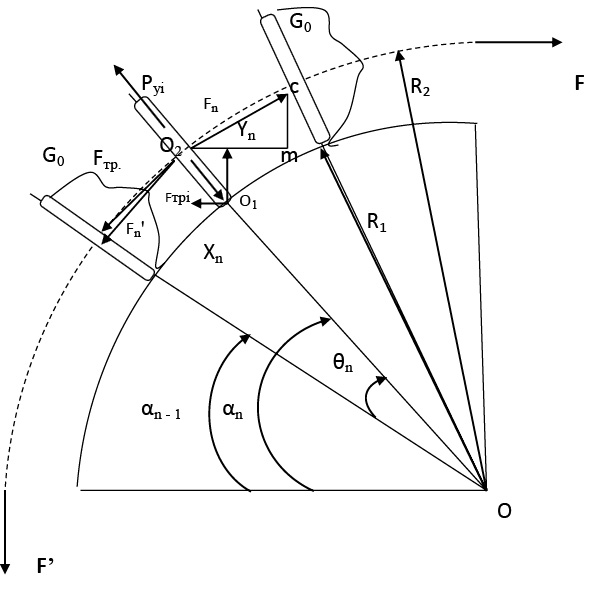
Рис. 4. Идеализированная схема нагрузки на поворотные рештаки
Исходя из геометрии проекция силы на ось У, действующей на скребок с номером n в шарнире соединения цепей со скребком справа от О2 :
Fny=Fn×Sin ((90o + θ)/2 – αn),
силы сопротивления части груза G0 на скребке и самого скребка при коэффициенте трения fтр
F тр.у =G0×fтр × Sin (90o – αn),
для силы тяги скребка слева от шарнира О2:
Fn’y = Fn’×Sin ((90o-θ)/2 – αn),
В направлении к центру поворота от центра массы О2 скребка и груза, приходящегося на него действует сила инерции определяемая вращательным движением с линейной скоростью v:
Руi= mпр×v/R2 ,
его смешению препятствует сила сопротивления Fтрi направленная к центру вращения, которую можно приближенно определить :
Fтрi= G0×f тр.
При существующей скорости транспортирования угля из лавы величина сила инерции будет не значительной. В решении не учитывается и трение торца самого скребка о рештак в месте опоры, хотя предполагаем, что прижимающее усилие при небольшом количестве рештаков и длине лавы около 200 м может быть существенной.
Тяговое усилие:
F = x1+x2+....xn+ F’,
F = y1+y2+....yn+ F’,
где – F’– часть тягового усилия для приведения в движение прямолинейной части конвейера. Сумма проекций сил действующих на скребки участвующих в повороте на оси Х и У, а также сумма моментов, например относительно точки О1 составленная для каждого скребка в общем случае определит выражения для VBA в Excel. В результате определяется нагруженность бортов рештаков и скребков на повороте, что позволит улучшить надёжность проектирования конвейера. Аналогичная задача, но с возможностью конкретизировать конструкцию к условиям работы представлена в пакете ADAMS, где рассмотрена группа рештаков, осуществляющих поворот, группа моделируется элементами (Link) из 3 –13 прикреплённых неподвижно к «земле» (ground) секций по поверхности которого движутся скребки по три на рештак. Скребки своим внутренним концом – опорой контактируют с гранями элементов моделирующих борта рештаков. Движение элементов рассматривается только в пределах каждого рештака, но поскольку они кинематические связаны через модель цепи, то учитывается полная группа рештаков в зоне поворота. Проектирование и испытания модели целесообразно начинать с создания минимального количества скребков, которые затем доводим до полного, что позволяет выявить особенности влияния, на характер движения конструктивных решений, включая неточности компоновки деталей. Скребки находятся в неустойчивом состоянии, поскольку сила тяги приложена к центральной точке возможного вращения скребка, опорные реакции в точках контакта с рештаком направлены по оси скребка и эти факторы не препятствуют колебаниям относительно шарниров. Создание всей поворотной системы не приводит к качественным изменениям в нагрузках. Графики опорных усилий при движении скребков под действием тяговой силы имеют периодический характер, рис 5.
Для скребка 3 в зоне установившегося движения имеем значения усилий изменяющих знак, что объясняем колебаниями бȯльшей чем на остальных амплитуды. Моделирование полной зоны поворота показывает, что проекции опорных усилий изменяются от максимума к минимуму и наоборот на каждом скребке. По длине зоны поворота проекции усилий на ось Х изменяются от минимума в зоне разгрузки конвейера до максимума в зоне привязки линейной части конвейера.
Выводы
Сопоставление аналитических и моделей и моделей на не авторских программных пакетах типа ADAMS зарубежного производства позволило выделить группу объектов (твердых тел и соединений) ADAMS, которые обеспечивают требования для моделирования подвижной системы из взаимодействующих элементов. При этом аналитические модели используются как дополнительные для тестирования отдельных моментов движения, а вся модель требует проведения испытаний характерных для сложных систем. Получены возможность использования моделей для класса рычажных механизмов входящих в системы горного оборудования крепей и угловых конвейеров.
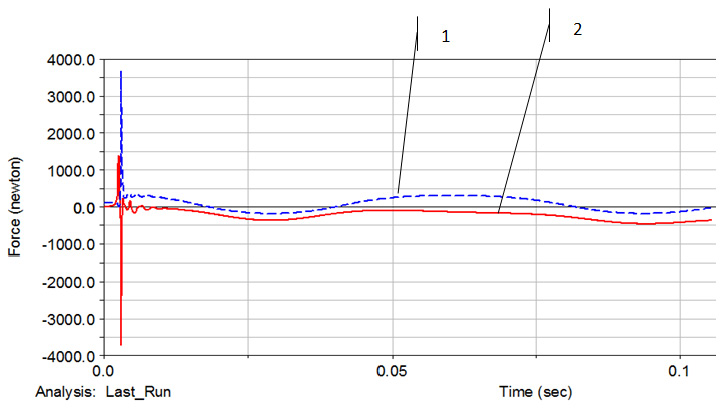
Рис. 5. Фото с экрана: кривые изменений опорных усилий вдоль оси Х в шарнирах скребков: 1 – третьего; 2 – второго
В идеальных схемах движения последних возникающие колебания обусловлены отсутствием сил трения сопротивления вращению скребка относительно центральной оси, к которой крепиться цепь. В реальности же вращению скребка препятствуют силы трения в шарнирах, скребков о элементы рештака и за счёт их “зарывания”, в транспортируемую массу. Сила же трения в опоре скребка на рештак, наоборот вызывает его наклон, за счёт момента от силы тяги, но этому препятствует пара сил, создающая момент, направленный в противоположную сторону возникающая за счёт того, что крепление цепей к скребку реально осуществлено в двух точках, а при повороте их межосевое расстояние определяет плечо пары сил, возвращающей скребок в исходное положение. По всему диапазону результирующие усилий в основном одинаковы, все скребки прижаты к внутренним бортам. Средняя нагрузка на опору скребка в зоне поворота определяется количеством скребков. Полученная совокупность моделей и расчетных выражений подтверждает работоспособность разработанных схем использования имеющихся и вновь разработанных конструкций, позволяет создать методики их автопроектирования.